We’ve talked about how technology has changed the way people buy homes and how they live in their homes, now let’s take a look at how the jobsite of the future will look. Technology will change the process of buying land, designing community master plans and designing home plans. Technology will change the way homes are constructed and the way construction is documented and accomplished.
Here’s a snapshot of what the future holds:
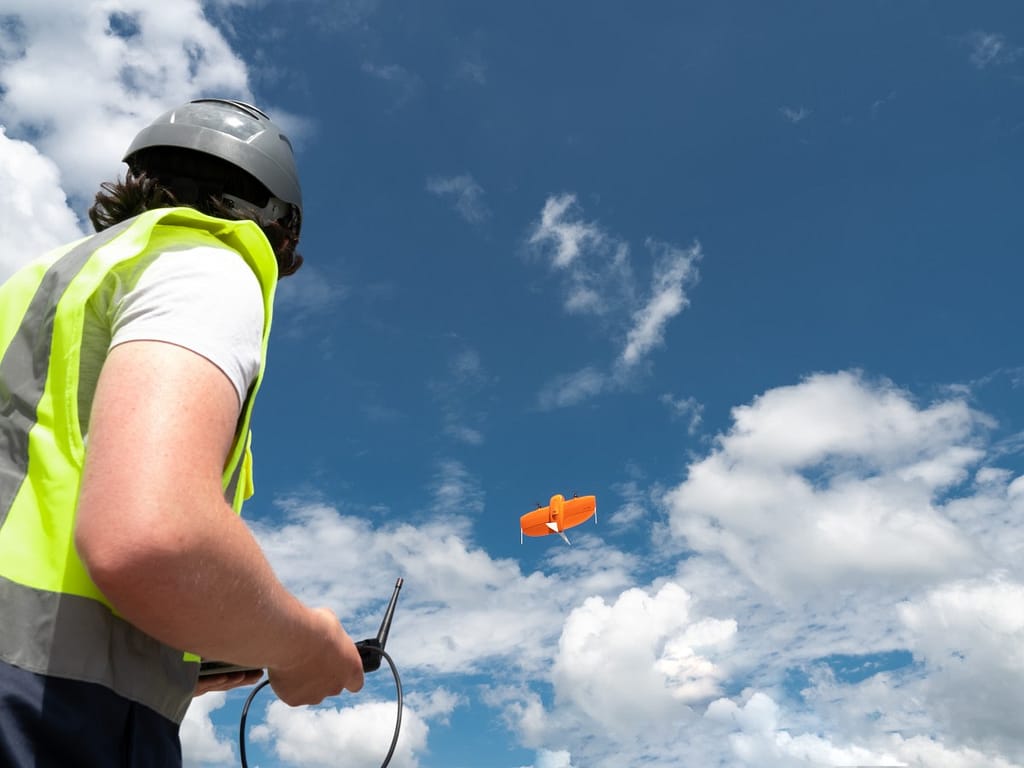
WingtraOne GEN II, a next-generation VTOL drone that offers industrial reliability and mapping versatility
with a new oblique camera configuration for high-quality 3D drone mapping data capture.
Before the land is purchased for our 2025 Home and the master planned neighborhood goes to the drawing board, a drone is used to fly over the land a developer is considering, sending aerial imagery to a data collection app.
During the design process, the use of Building Information Modeling (BIM) software provides space for collaboration. Each member of the design team can add their piece to the same model –no more multiple versions of a 2D paper drawing. The model evolves immediately as people contribute, streamlining the process and increasing efficiency. BIM also helps with problem solving in the design and planning stages of a project, by automating clash detection. A complete picture of the project is accomplished using virtual reality technology to allow a walk-through of the project before it’s ever built. Job scheduling and budgeting tools are used to reduce expenses and inefficiencies.
Many of the components going into the home are built off-site inside of a factory environment with complete or semi-complete assemblies shipped to the jobsite. On site, Engineering Cementitious Composite (ECC) or “bendable concrete” uses less cement, while the small polymer-derived fiber in the mix makes it stronger and more crack-resistant than traditional concrete. Nanomaterials function as a substitute for steel reinforcement in structures and foundations. A 3D printer onsite extrudes various components—both structural and aesthetic. Aerogel, a foam-like solid that holds its shape despite being 99.989 percent air offers two to four times the insulating power of traditional fiberglass or foam insulation. Robotic labor includes the Australian Hadrian X, capable of completing brickwork on a home within 1 to 3 days, laying 1000+ standard bricks per hour.
Subcontractors and inspectors use technology to deliver and document faster and more accurate data. Drones inspect hard-to-reach places. Wearing smart glasses integrated with a remote assistance platform, a site contractor converts visual data into documents, taking photos and videos. He uses voice commands to do all these things and receives back visual instructions or videos with all the steps that need to be performed to complete the installation or repair he is there to do.
Data collection app users report more than 20 field and administrative hours saved each week and a 50 percent reduction in data entry errors. –DeviceMagic
below: Wearable technologies from VSight include Supported Smart Glasses
A data collection app sends information from the field to all collaborators for review analysis and legal documentation. Daily construction reports, safety assessments, quality inspections, timesheets, punch lists – are all completed on mobile devices, submitting and logging data instantly. Data collection workflows are automated so the next step in the job is scheduled. Submission of one form triggers another form to be sent until a task is completed with all necessary sign-offs and documentation to prove progress or completion.
All of the technology mentioned in this article already exists and is in use on construction sites already. The question is: Which ones will become mainstream and when? Advancements take time to be adapted and are not without challenges.
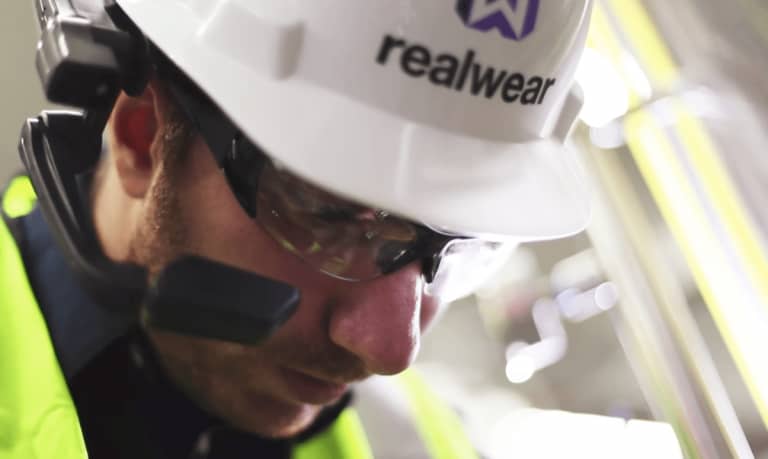
One example of a “modern world” problem is the conflict between drone pilots and regulations designed to protect surveying professionals. The Board of Examiners for Engineers and Surveyors has taken legal action against drone companies in several instances across various parts of the country, accusing drone pilots of “surveying without a license.” Surveyors would need Federal Aviation Administration approval to professionally fly drones, and drone operators would need to pass state licensing exams to produce legal surveys. It certainly makes sense for partnerships to be developed between drone operators and engineering or surveying firms; until these partnerships become more commonplace, legal professionals have advised drone pilots providing real estate data to add disclaimers to any data they supply to say, “their maps are not meant to replace surveys that are often needed for mortgages, title insurance and land use applications.”
The Bottom Line: Tech has disrupted every industry, so it’s no surprise that the construction industry is following suit.